New to the world of stick welding? If the answer is yes, read this article and use it to gain a basic understanding of one of the most popular welding processes in use today. The first thing to be aware of is the electrode. It’s not wire. No, welders use a special flux-coated electrode, a consumable rod that incorporates all shielding and oxidation prevention elements. Wrapped up under this coating, filler metals fluidize when exposed to weld heat.
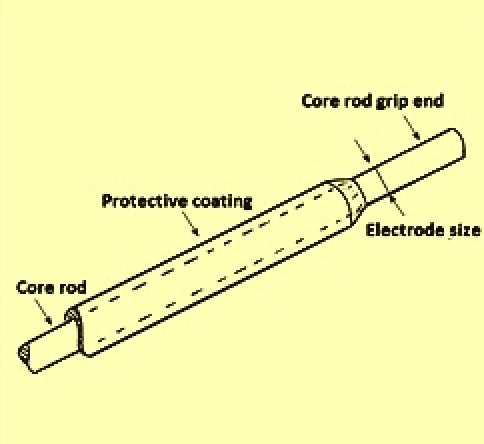
Coated Welding Electrode
Source: https://www.ispatguru.com/electrode-quality-steel-for-core-wire-of-covered-electrodes/Coated Welding Electrode
There are obvious advantages to discuss, and they’ll be covered in greater detail later in this post. Foremost among them, there’s no need for shielding gas, not when the flux coating contains special oxidation protecting additives. As the flux coating melts, it’s transformed into a gas, and this gas displaces air.
Stick welding (also known as Shielded Metal Arc Welding or SMAW) isn’t difficult to learn, but it is difficult to master because the flux and stick metal combine in unpredictable ways to produce a higher-than-average deposit of slag.
SMAW
Source: https://en.wikipedia.org/wiki/Shielded_metal_arc_welding
Learning The Basics: How to Stick Weld Efficiently
The arc is struck, the Stick welding/SMAW spark lights up above the base metal. Equipment settings are correct for the alloy type and metal thickness. A dual-voltage Tooliom TL-195S Stick Welding machine has been picked for the job. It’s capable of welding mild steel thanks to its maximum output rating of 195A. The time-honored welding technique starts with the hand of the welder adjusting the angle of approach slightly. An optimal arc length of between 3 to 6mm is established as the electrode is pulled back. A push pattern isn’t advised, not when there’s so much slag forming around the weld; there’s a good chance this ugly deposit will make its way into the weld pool and contaminate the cooling weld if pushed.
There’s a bumpy learning curve ahead. The diameter of the electrode is going to impact arc length, as will the fillers and additives coating it. The secret to minimizing weld spatter is in keeping the arc distance short. Arc stability is going to increase if this approach is taken, but then the issue of spatter is still going to cause problems. Of some help here, the Tooliom TL-195S includes a welcome spatter minimization feature. Good to know, especially when the other solution is a reduction in arc-to-workpiece distance. When this happens, better arc steadiness is likelier, but the downside is more slag. Maybe that’s why stick welding is regarded by many as a game of give and take, of balance and tradeoffs. Still, the implementation of slag reducing equipment can only help the situation.
Stick welding has that one popular benefit over other welding techniques. We’re, of course, referring to the fact that stick welders can work outdoors in windy environments without worrying about weld pool contamination. Without need for a bulky cylinder of shielding gas, there’s no gaseous, oxidization protecting envelope to blow away from the weld. Even so, as each pass is made, some slag will collect. Here’s the next downside to cover when stick welding, then. Relatively fast to make, a pause will be needed after each pass cools. That’s when the chipping hammer and wire brush are pulled from the welders’ tool kit. To underscore the importance of this step, it may introduce productivity hampering time stoppages into a job, but that’s just part of the realities of a stick welder’s life. The slag and spatter must be removed before a second or third pass can be made.

Describing a Standard Stick Welding Equipment Rig
A coated stick is fitted into the electrode holder. An angle is decided upon, a distance set, and a uniform weld bead is controlled by pulling it away from the weld puddle. The equipment is built for stick welding, with the electrode lead typically plugged into the negative terminal of the equipment. A Tooliom multi process welder TL-200M is another worthy candidate for the work, with its 3-in-1 feature incorporating a stick setting. There’s an electrode holder lead in the box, too, so all that’s left to do is select the correct electrode and fasten the earth clamp. It’s attached to the workpiece to complete the electrical circuit that makes arc generation possible.
MIG/Stick/TIG Multi-Process Welder TL-200M 3 in 1 Welding Machine|Tooliom
Multiple weld positions, including flat and vertical, are possible with a modicum of effort when stick welding, but that’s only true if the welder selects a stick electrode that corresponds to the required weld position. To review, then, equipment with a stick welding mode and the correct leads must be supplied. Lead one is an electrode holder. Lead two is the ground clamp. It’s the return line for the electrical current. Don’t treat this component poorly, for a secure ground clamp equals a high conductivity return circuit. Arc steadiness is assured when the weld distance gap and ground clamp are both maintained properly. With all of that covered, the question of electrode type isn’t going to be covered here. Stick electrodes play a significant role in the process. They deserve a whole section to themselves.

Not only utilized as fluidized filler and weld pool metal, electrodes are coated in special additives. They melt into the pool and take flight above the weld area, functioning as site shields. They begin solid, enter a gaseous state, and cool as part of a strong weld. They’re rather complex welding assets, labelled as they are with multi-digit codifiers.
Introducing the Basics of Stick Electrode Selection
The current and voltage are set. The gauge and type of alloy are looked up in a data table if the settings aren’t already decided upon. Set to DCEN (Direct Current Electrode Negative), which is just tech-speak for negative polarity, the characteristics of the arc are biased towards thinner metal work and a smoother, flatter weld bead that strikes easily. High DC currents and dual voltage (110V/220V) operation is decided upon by the welder to accommodate the project in question.
Direct Current Electrode Negative(DCEN)
Source: https://awo.aws.org/glossary/direct-current-electrode-negative/
Now that all the equipment settings are locked in, let’s talk about stick electrodes. They’re not all created equally. That’s an important point, as there’s a whole collection of these electrode classes to sort through. Without some kind of coding system, it would be impossible to find a stick that’s a fit for a specific project. To that end, there’s a stick classification system in place. America uses the ‘E’ prefix, and it’s a globally recognized standard, so we’ll use it to illustrate a few well-known examples in the industry.
-
First pair of digits - Indicates the tensile strength of the core metal. This is the filler metal. Higher numbers equal more weld strength.
-
Third digit - Covers the weld position. Three numbers are used. 1 is all positions, 2 is flat and horizontal, and 4 is vertical down and overhead.
-
The fourth digit - Part of a list of possible flux coatings combined with polarities
A second list has been appended to the first. It covers some commonly utilized electrode codes.
E6010 - Renowned for producing welds with deep penetration. Superior arc stability and multi welding position versatility. Works well on carbon steel and on low alloy steels. It does solidify quickly, so it’s not the best option for beginners.
E7018 - Refined medium penetration welds are achievable with this flux-covered solution. The third digit still assures all-position welding, and the weldable base metals are much the same as 6010, although this electrode type is the preferred candidate for working on stainless steel.
E7024 - Offers higher deposition rates and excellent weld bead aesthetics thanks to its iron powder coating. It’s a fine structural welding electrode that’s commonly used in bridge building and heavy industry projects.
E7048 - Designed for vertical down welding, the low hydrogen flux defies weld cracking and mechanical stresses. The electrode melts easily but solidifies rapidly, hence its use in vertical down applications. Features fast slag cleanability and excellent crack resistance.

Source: https://www.familyhandyman.com/article/heres-what-you-need-to-know-about-stick-welding-pros-cons-cost-and-more/
Beginners Take Note: Considering Pre-Welding Job Variables
Find a piece of scrap metal to weld. This is one of the best pieces of advice a stick welder can impart. First things first, know the base metal, its thickness, its geometry, and its metallurgical properties. From there, a scrap piece of metal with the same properties can be worked upon until a stick welder has earned his title. The cooled joint should be clean and relatively free of slag. If multiple passes are used, multiple cleaning will be done, each one after a pass has been made.
Besides practicing a fine-tuned pull pattern that won’t drag slag into the weld puddle, there’s the option to perfect a gentle circling motion as well. The electrode is gently manipulated in an outer spiral, widening the bead so that it fills the weld fillet. Reserve some time to set equipment settings, too. The holder lead will likely be plugged into the negative connector, just as it states in the Tooliom manual. An E6010 stick electrode is a good day-to-day weld pool and flux shielding solution, but we advise welders to expect more from themselves. Consult a chart of common electrode classes, select one that suits the project, and realize that although this is one of the most established welding techniques known, we always have the opportunity to improve on what has gone before. That message applies doubly so when the equipment available has technologies and capabilities built directly into its inner workings, just like the Tooliom TL-200M 3-in-1 welding machine has in abundance. Synergic control, that’s the signature feature we’re referring to, by the way.
MIG/Stick/TIG Multi-Process Welder TL-200M 3 in 1 Welding Machine|Tooliom
Expect to consult stick electrode charts for classification codes that suit various base metals. Otherwise, stick welding is incredibly versatile; it’ll weld most ferrous alloys and quite a few non-ferrous metals as well. Titanium isn’t one of them, unfortunately. Galvanized steel will stick weld, but a smart welder should know enough to grind off the zinc layer before starting.
Other than cleaning and other basic prep work, like grinding and selecting the right electrode, there are pros and cons to consider. As an initial benefit, yes, the process works outdoors, even if it’s breezy. The stick additives tune the process into the requirements of the job, so that’s another benefit worth mentioning. In the cons column, there are productivity issues to drag the process down. Slag accumulates and needs cleaning. This’ll slow the work to a grind. Also, although it requires some skill, the work will rarely look as good as a job done with TIG gear.
Final Analysis: The Popularity of Stick Welding is Well Justified
This technique is etched into the DNA of welders. It doesn’t really matter if it’s referred to as SMAW or stick welding; it’s the steadfast and enduring nature of the process that counts. The technique does have flaws, does produce slag and does sometimes incur more productivity hits, but there’s no arguing against its biggest benefit. Stick welding simply works, and it does so on construction sites and open-air settings. There’s no cylinder of shielding gas, just the simplicity of an electrode holder and an intelligently selected flux-coated electrode. The numbers coded into those sticks convey everything from weld position to the filler flow properties, too.
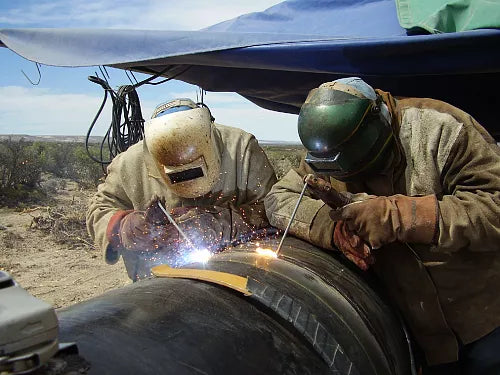
Source: https://www.canadianmetalworking.com/canadianfabricatingandwelding/article/welding/welding-automation-takes-hold
Accessible to all, there is a learning curve to overcome, and there are occasional bumps to overcome during the journey to stick welder master, but a steady hand and the foundations set by the provision of a solid stick welding equipment package quickly smooths the way.
Conquering the Learning Curve: A Timeline for Stick Welding Proficiency
Time Period | Skill Level | Activity Focus Area | Outcome |
First 2 months | Beginner | Stick welding principles. Introduction to safety procedures | Basic process knowledge. Safety awareness. |
Beginner | Learn equipment settings. Learn about stick electrodes | Awareness of electrode properties | |
Beginner | Basic joint preparation. Welding positions. | Ability to prep joints and weld them | |
Month 3 and 4 | Novice | Practice striking the arc and maintaining it. | Consistent weld bead manipulation |
Novice | Welding on scrap pieces of metal. Learning different alloy properties | Familiarity with several easy weld positions | |
Novice | The welder begins to pick up bead control and slag minimization skills | The beginnings of high-quality welding. Angle and distance control. | |
Novice | The ability to troubleshoot stick welding defects | Identification and resolution of stick welding issues |
Beyond those initial months, intermediate stick welding territory awaits. Vertical welding techniques can be tackled with confidence.
Welding Primer Series 4: Stick welding Made Simple - FAQ
Q: What is the primary advantage of using a flux-coated electrode in stick welding?
A: The primary advantage of using a flux-coated electrode is that it eliminates the need for shielding gas. The flux coating contains special additives that provide protection against oxidation, and as the flux coating melts during welding, it transforms into a gas that displaces the air, creating a protective atmosphere for the weld.
Q: Why is it important for beginners in stick welding to practice on scrap metal?
A: Practicing on scrap metal is important for beginners in stick welding because it allows them to become familiar with the base metal, its thickness, geometry, and metallurgical properties. It also helps in honing welding techniques, including maintaining a clean and slag-free weld, achieving a consistent weld bead, and perfecting electrode manipulation.
Q: What is the basic process of starting a stick welding arc?
A: To start a stick welding arc, you strike the electrode against the base metal. As the arc is struck, a spark lights up above the base metal. It's important to have the correct equipment settings for the alloy type and metal thickness. An optimal arc length of between 3 to 6mm is established as the electrode is pulled back. Pushing the electrode is not advised due to the slag formation.