This article will discuss the basics of welding processes: MIG, MAG & FCAW.
The MIG, MAG & FCAW are continuous welding processes (not intermittent like SMAW shielded metal arc welding due to the need of charging new electrodes) in which the welding pool is protected from the surrounding atmosphere by using shielding gases (in addition to flux in case of FCAW), which flows from the welding torch on to the piece to be welded.
The continuous characteristic of wire feed makes these processes highly productive as compared to traditional TIG and SMAW welding processes, so these processes are used in heavy industries like shipbuilding, steel structures and automotive industries.

Photo by @snowmandawelder
What do MIG, MAG and FCAW mean?
MIG is an acronym for metal inert gas.
MAG is an acronym for metal active gas.
MIG and MAG are also known as wire welding or gas metal arc welding (GMAW) in which solid wire is used in welding. This is one of the most popular welding processes after shielded metal arc (stick) welding. As the thickness of the metal surpasses 18 gauge, you will need to switch to .030 size wire. A .030 ER70S-6 wire will cover most of your welding needs,but for steel over 3/16”, you will need a .035 wire.
TOOLIOM ER70S-6 Mild Wire for TL-200M/TL-250M Pro
FCAW is an acronym for flux-cored arc welding in which a flux-cored wire (not solid wire as in the case of MIG & MAG welding) is used in welding.
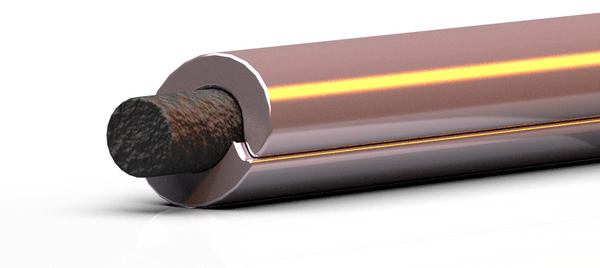
Source: http://weldnotes.com/?p=123
MIG is usually used along with or confused with MAG; however, the two procedures differ as follows:
|
MIG welding |
MAG welding |
FCAW welding |
Meaning of Acronym |
Metal inert gas welding |
Metal active gas welding |
Flux cored arc welding |
Uses and Applications |
MIG welding is used for stainless and mild steel and non-ferrous metals including aluminum and aluminum alloys, titanium, and copper. |
This process is used for welding low-alloyed construction steels and is suitable for welding a wide range of materials thicknesses starting from thin sheets to medium and thick sheets. |
FCAW is an acceptable welding process to be used in structural steel fabrication, oil and gas industries, pressure vessels fabrication, pipe lines works and it is suitable for a wide range of materials including, mild steels, alloy steels and nickel-based alloys. |
Shielding Gases used |
The inert gases argon, helium, or a mixture of both gases are used as the gas, as they do not react with the material. |
Active shielding gases like CO2 gas or a mixture of gases which consist of a mixture of argon or helium with carbon dioxide or oxygen are used. |
Active shielding gases which may be carbon dioxide or blends of argon (75%) and carbon dioxide (25%) |
How do MIG, MAG and FCAW work?
The MIG, MAG and FCAW are very similar welding processes and as shown above, the difference comes from the used shielding gas and whether the welding wire is solid or flux-cored one.
As these processes are arc welding processes, the source of melting energy comes from the electrical arc which is established between the welding wire and the workpiece, and the welding pool is protected by using a shielding gas that is applied on the weld pool through the welding torch.
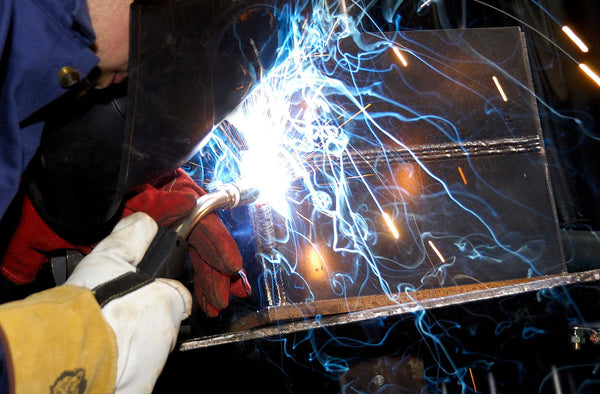
Source: https://www.twi-global.com/technical-knowledge/job-knowledge/mig-welding-004
When the source of heat (the electrical arc) is removed, the weld pool cools down, solidifies, and forms a new piece of molten metal which is called the weld metal.
The process of wire feeding is a continuous one in which the wire feed speed depends on the melting rate which mainly depends on the welding current and voltage used in welding.
Here below is the layout of MIG, MAG and FCAW welding processes:
MIG and MAG layout
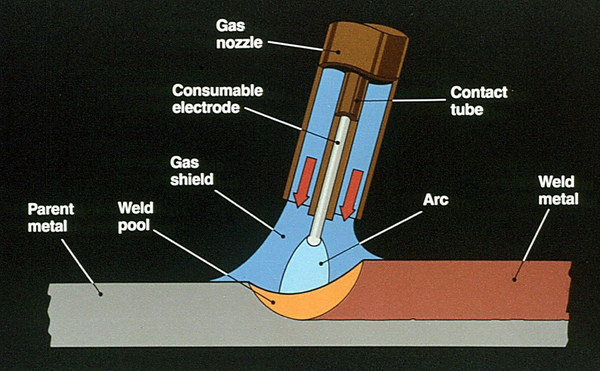
Source: https://www.researchgate.net/figure/GTAW-welding-Courtesy-TWI-For-carbon-steel-base-metal-number-ie-P-No-is-1-and_fig2_308174944
As shown, the wire is solid and the shielding gas is applied through the welding torch toward the welding pool.
FCAW layout
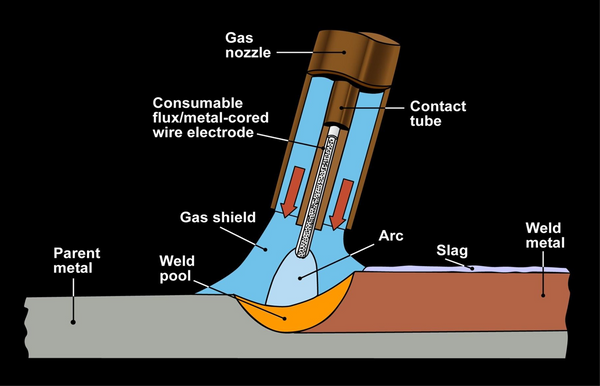
As shown, the welding wire is flux-cored or metal-cored. In this process, the molten weld metal is protected by the applied shielding gas which goes to the welding pool through the welding torch and is also protected by the emitted gases coming from the burnt flux. That is why it is sometimes called “OUTERSHIELD” process. That is why it is characterized by the high quality of produced weld metals. This process can also be operated without using shielding gas, and in this case, the protection of the weld pool comes from the flux only. That is why it is called “INNERSHIELD” process, which can be used in applications where the setup of shielding gases becomes difficult, like welding at high Heights.
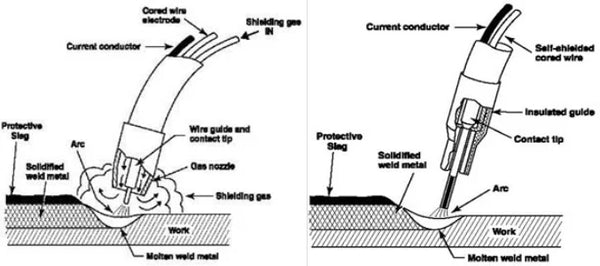
OUTERSHIELD Vs. INNERSHIELD process
Last but not least, you can check out this linked article Flux-Cored Arc Welding(FCAW)Basics to get more information about FCAW.