Worked iron has literally been around for centuries. That’s something that can’t be said for many other metals. Only a few other historically familiar metals, such as copper, tin and bronze can lay claim to a similar lineage. All things being equal, cast iron should then be easy to weld because it’s been around for so long, but that’s not necessarily true. For one thing, its composition includes a high percentage of carbon, making it susceptible to stress cracking.
If the popularity of this carbon-heavy alloy had waned over the years, there wouldn’t be a problem. An occasional specialized welding project would yield satisfactory results, then the welder would shift back to a more familiar metal stock like stainless steel or mild steel. However, cast iron products are still common. They’re present in the automotive industry, in decorative elements such as ornate fences and gates, in railways, industrial machinery, pipes and fittings, and countless other everyday applications. There’s no getting around it, cast iron is everywhere, which means welders deal with its unique material characteristics on a daily basis.
Cast Iron Part - FCA 3.0L V6 Diesel Cyl Block
Source: https://metalcastinginstitute.com/cast-iron-automotive-applications/
Why is Cast Iron Difficult to Weld?
It’s a simple question. Is there a simple answer? In olden times, this was a metal that was full of impurities. The presence of silicon, manganese, trace quantities of sulfur and phosphorus all contributed to a range of undesirable welding characteristics. Welds crack, the metal becomes brittle, and the workpiece distorts if arc heat isn’t managed. Why, then, are these impurities allowed to persist? Some remain stubbornly in the ore after it has been mined. Some impurities are added during the casting operation to aid in the metal’s fluidization so that it conforms to the shape of the casting. Others are added to reduce iron oxidation or to improve machinability.
Hot Cracks
Source: https://weldguru.com/welding-cracks/
The point is, although desirable when making a casting or when pressing a cast iron piece into service, those same properties can and often do undermine a welding operation. The part expands and cracks because the inflexible metal expands too quickly when exposed to heat. And, although gifted with augmented hardenability and ductility, the addition of 2 to 4% of carbon does potentially introduce an increased risk of workpiece brittleness. By the way, the appearance of phosphorous in the composition of the metal acts as yet another brittleness agitator. Unfortunately, iron ore and coke-fueled furnaces are known for introducing traces of phosphorous.
Ultimately, the alloying carbon and trace impurities are there because of the mining work, the furnace treatment stage, and the casting work. They don’t impact the performance of the alloy too much when its cast and utilized, but the opposite is true when the metal requires welding. The alloy might crack, might turn into a weak, brittle joint around the fusion site, and it may experience some small amount of parts distortion, too. As welders, as professionals or hobbyists who are tasked with a cast iron welding project, we must accept these risks and learn to deal with them.
Incorporate a Pretreatment Mindset When Welding Cast Iron
As a base metal stabilizing step, it’s critical that the workpiece is slowly heated before the welding process starts. A furnace is the best option, one that’s easy enough to source if the work is being done in a workshop or a metal fabrication factory of some type. If this is field work, the solution is a little harder. Granted, an acetylene torch is good for localized heat, perhaps as applied to a small piece of cast iron. That’s not a practical solution for larger parts. The preheat operation must be applied uniformly. If the heat isn’t applied evenly, localized material stresses develop in the metal, cracks propagate, and the job ends with a mess of micro-fractures.
Preheating Cast Iron
Source: https://weldguru.com/cast-iron-welding/
Fortunately, there are devices designed for exactly this role, devices that uniformly preheat entire cast iron pieces, completely and volumetrically. One such device is an induction power system. It’s not worth getting into the technical principles behind this machine in too much detail, not in a welding article, but suffice to say its operating principles are based on electromagnetic fields, on the generation of heat as an upshot of flux-produced eddy currents.
Heated to between 260°C and 650°C by use of a furnace or one of the two other heat sources mentioned in previous paragraphs, the goal is to keep the cast iron part below its austenitic temperature. Heated too much, the iron microcrystalline structure transforms to a different state. Obviously, that’s not a desirable outcome here, not for welding. Incidentally, this temperature spread is unusually wide. To explain that wide temperature gap, welders should remember that there are different types of cast iron stock. Here’s a shot list of alloys welders can expect to encounter:
-
Gray cast iron - Brittle yet crack resistant, the alloy incorporates flaky graphite molecules, hence its gray coloring. Characteristics associated with this metal include increased wear resistance, low ductility, and high thermal conductivity.
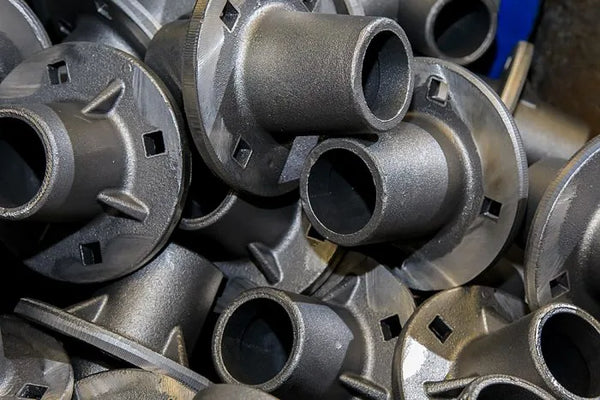
Source: https://www.ferroloyinc.com/gray-iron-castings/
-
White iron - Highly wear resistant, this flavor of cast iron is logically more brittle than other members of its family. There are hard carbides in its composition, which reduce its weldability. Nickel-based fillers improve this feature somewhat.
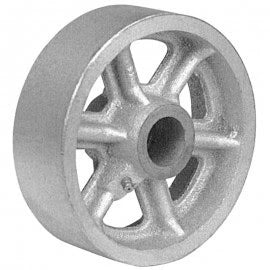
-
Ductile - Augmented with magnesium to create spherical graphite nodules. Offers superior tensile strength, but metallic toughness comes at the cost of greater brittleness. It’s generally more weldable than gray.
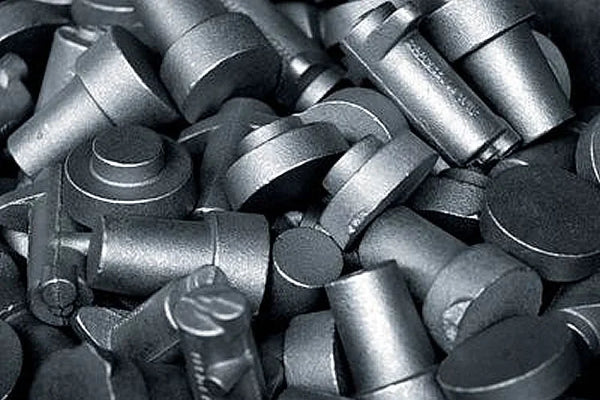
Source: https://www.castermetal.com/ductile-cast-iron/
-
Malleable - Unusual for cast iron, its malleable form is deformable to some extent, and it will bend. As it’s a ductile metal, it won’t crack as readily as other types of cast iron. Weldable, but a preheat phase is still recommended.
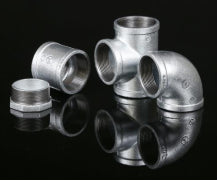
Source: https://www.malleableiron-pipefitting.com/industry-knowledge/difference-between-ductile-iron-malleable-iron.html
There are several additional cast iron types, but the above four are more than enough to go on for the moment. They mix crack causation and brittleness imbuing factors with material rigidity in some cases, while other forms introduce desirable levels of malleability and enhanced ductility. Weldability is, of course, the most important aspect, and it does vary considerably between all four of these alloy types.
Selecting the Best Welding Technique: How to Weld Cast Iron
Only one process/equipment build comes to mind when a cast iron welding job crops up, and that option will be discussed in a moment. What can be stated with some confidence is that several techniques do not work well with cast iron. MIG welding is one, for it injects weld beads with copious quantities of thermal energy. Even with preheating, that means a sharp shot of thermal stress to a brittle metal base. Cracks will form and need expert remediation work.
If this is the chosen welding technique, use specialized flux-cored wire and nickel-based fillers to help control the migration of carbon from the base metal into the weld, thus reducing the risk of brittleness. As a best-case scenario, opt for a MIG/Stick/TIG Multi-Process Welder TL-135M. The MIG functionality is there, but there’s an elective MMA (Stick) welding mode, too. MMA, Manual Metal Arc, welding with an E7018 electrode removes the need for a cylinder of shielding gas while delivering an iron-rich filler.
MIG/Stick/TIG Multi-Process Welder TL-135M 3 in 1 IGBT DC Inverter|Tooliom
Better yet, there are electrodes that are expressly designed as high-performance cast iron fillers. They’re nickel-based and include candidates like the nickel-heavy ENiFe-CI and the ENiFe-G. As for how to choose the right electrode for a particular cast iron welding job, there’s a whole list of job criteria to wade through before the electrode is locked in by the welder in chargge. Is this repair work or cast iron fabrication? Is plasticity an issue? What about the weld position and the type of cast iron?
If the welding project is switching to a more specialized electrode type, let’s make the jump to a high-functioning Tooliom MIG/Stick/TIG Multi-Process Welder TL-200M 3 in 1 Welding Machine. MIG and TIG modes are clearly marked on the control panel, as is the synergic control feature. Amperage and voltage settings are critically important, as cast iron is sensitive to heat-related expansion issues. Arc consistency is also key, so maintain the bead with a “pull” motion. The likelihood of brittle metal zones around and in the joint will increase if the bead travel speed is too slow. The same can be said for cracks and workpiece deformation, so a consistent travel speed becomes even more critical. A balance must be struck, though, for the fluidized weld puddle has to penetrate deep, all the way to the root.
MIG/Stick/TIG Multi-Process Welder TL-200M 3 in 1 Welding Machine|Tooliom
Weave and stringer bead motions are maintained to ensure the nickel filler fully occupies the weld seam. Depending on the joint profile and workpiece thickness, multiple passes might be in order. Likewise, that choice of motion will depend on the groove profile and thickness. Again, preheating is a necessary part of the work, but so then is a matching cooling stage. There might even be a need to bring in some kind of insulating material or a cooling blanket to ensure a predictable cooling rate. In heating the cast iron, the risk of thermal stress is minimized. In cooling it, the welder prevents thermal stresses from being “locked” into the workpiece. It’s a little like a localized heat treatment process, with the welder acting as both the furnace controller and the tempering technician. That’s an easy enough proposition in a fabrication yard, where furnaces and cooling fans are readily available, but it’s a good deal harder to implement in the field.
Avoiding Common Mistakes When Welding Cast Iron
Common mistake number one is the decision to skip the preheat phase. Yes, it is possible to cold weld cast iron, but a steeper thermal ladder is to be expected when working cold. That’s a workable option on malleable metals, but it’s going to cause problems on white iron, which is the material that contains hard carbides. Lower machine amperages help, but then there’s lower depth penetration, which isn’t good for thicker workpieces. Cracks will form. While sealing compounds can take care of most cracks, this isn’t the ideal solution. If possible, there should be some preheating.
MIG Cold Welding Cast Iron Process
Source: https://www.weldingtipsandtricks.com/cold-welding-cast-iron-with-mig.html
Next in the troubleshooting list, expert welders will be aware, DIY enthusiasts less so, of that age-old problem known as excessive spatter. Fortunately, nickel electrodes don’t produce too much of this messy bead waste. And there’s better news, the welder is already managing the synergic controls on the Tooliom TL-200M, so the amperage and arc length parameters are naturally biased towards a cleaner, more aesthetically pleasing weld bead. Along with groove preparation and preheating, the welder will have also scraped away any oil, paint and corrosion from the cast iron.
That latter issue is common when working on repair projects. Let’s say an attractive cast iron railing needs to be fixed because one of the linkages holding it in place has fractured. It’s likely covered in paint and rust; cleaning of the entire area in and around the weld zone is necessary before the equipment is pulled out and set up.
Remove Rust Before Welding.
Source: https://www.youtube.com/watch?v=kzbcVb2UymA
There are, of course, numerous weld defects that’ll be picked up during the course of a welder’s career, and that’s an especially accurate truism if the welder spends a lot of their time on cast iron. There’s going to be a lot of repair work, as old ironworks are everywhere. Then there’s carbon-infused brittleness and cracking, which is a natural upshot of the metal’s hard, inflexible nature. As stick welding gear is popular with cast iron jobs, there’s more spatter to clean up. And all of this is just for the defects caused during the welding process. What about the post-weld work?
Post Weld Stress Reduction and Cooling in Cast Iron Welding
Forced air cooling actively aids heat removal, as does the strategic positioning of electric fans. If performed in a factory, there’s even more control available in the form of cooling chambers. Then again, what if the welded cast iron component is still loaded with traces of residual stress? Cracks will propagate, the workpiece will warp and its dimensions will alter over time. Before any of that can occur, a secondary heat treatment operation can be performed to release those stresses. Again, that’s a job best left to the auspices of the welder during the post welding phase of the job.
Source: https://weldinganswers.com/what-is-stress-relieving-and-why-we-need-it/
Thanks to experience, hidden stresses should be caught before they produce cracks. Otherwise, the whole job might become an expensive exercise in futility. As with many other welding techniques and jobs, it’s always a good idea to practice on a scrap piece of metal. In this case, a chunk of cast iron is utilized. Even if it’s not of a comparable size to the project piece, its geometry should be similar.
Concluding Thoughts: It’s A Myth That Cast Iron Isn’t Weldable
And there we have it, thanks for sticking with this article to the very end. It’s been a rough ride, but we’ve determined that cast iron, in all of its forms, is weldable. It’s not a hard alloy to get good fusion results from. It’s more that the results can be unsatisfactory due to the varying degrees of brittleness that are expressed by cast iron after it cools. To avoid that outcome, we rewind the process all the way back to the job inception phase. It’s here that preheating smooths sharp thermal shocks until mechanical stresses are minimized.
Bookending the process, an equally important cooling phase stops residual forces from being locked inside the cast iron microcrystalline matrix. Technique is important, as is the selection of an excellent multi-functional welding machine. It is possible to MIG weld the metal, but the already rigid material doesn’t require much arc energy to shift to its brittle state, where it’ll crack and weaken. Stick welding, aka MMA, is the mode that we select on the Tooliom TL-200M 3 in 1 welding machine. It’s controllable, capable of accepting nickel loaded electrodes, perfect for cast iron work, and it can shift its arc energies responsively to cancel out the heat overloads that cause parts weakening embrittlement.
MIG/Stick/TIG Multi-Process Welder TL-200M 3 in 1 Welding Machine|Tooliom
By employing proper welding techniques and addressing any detected stresses, and by incorporating a potent pre/post treatment stage, too, welders ensure quality welds. Moreover, timeless cast iron welds can be every bit as strong and reliable as joints achieved on modern alloys.
TIG Welding Cast Iron
Source: https://www.weldingtipsandtricks.com/tig-welding-cast-iron-409.html
A Tabulated Summation of How to Weld Cast Iron
Summary | Key Information | Additional Details | |
Introduction | Cast iron is challenging to weld due to impurities and high carbon content. | Historical significance of cast iron | Challenges in welding cast iron |
Why is Cast Iron Difficult to Weld? | Impurities make cast iron prone to welding issues. | Impact of impurities | Impurities include silicon, sulfur, and phosphorous |
A Pretreatment Mindset | Preheat the workpiece to minimize cracking. | Importance of preheating | Methods for uniform preheating |
Types of Cast Iron Alloys | Cast iron types include gray, white, ductile, and malleable | Different cast iron alloys | Properties and characteristics of each alloy |
Selecting the Best Welding Technique | MMA welding with specialized nickel electrodes. MIG welding with nickel wire. | Challenges with welding modes. | Recommended techniques and equipment |
Avoiding Common Mistakes When Welding Cast Iron | Preheating, managing spatter, and cleaning to avoid welding defects. | Common welding mistakes | Tips to prevent defects and ensure quality |
Stress Reduction and Closing Thoughts | Proper cooling and post-weld heat treatment can relieve residual stresses and prevent cracks. | Importance of post-weld steps | Techniques to release residual stresses |
How to Successfully Weld Cast Iron - FAQ
Q: Why is cast iron difficult to weld?
A: Cast iron is challenging to weld due to several factors, primarily related to its composition and historical use. It contains a high percentage of carbon, making it susceptible to stress cracking. Additionally, impurities such as silicon, manganese, sulfur, and phosphorus present in cast iron contribute to undesirable welding characteristics. These impurities can lead to issues like weld cracking, brittleness, and workpiece distortion if the heat during welding is not carefully managed. Despite these challenges, cast iron is still widely used in various applications, making it necessary for welders to deal with its unique material properties.
Q: How can pre-treatment be incorporated when welding cast iron?
A: Pre-treatment is a crucial step when welding cast iron. It involves slowly heating the workpiece before the welding process begins. A furnace is the preferred method for preheating in a controlled environment, but in the field, localized heat can be applied using an acetylene torch. Regardless of the method used, it's essential to apply heat uniformly to avoid localized material stresses, crack propagation, and micro-fractures. Special devices like induction power systems can be employed to achieve uniform preheating of entire cast iron pieces. The goal is to keep the cast iron part below its austenitic temperature to prevent undesirable structural changes.
Q: What are the common types of cast iron alloys, and how do they differ in weldability?
A: Cast iron comes in various alloys, each with its own characteristics and weldability. Some common types of cast iron alloys include:
- Gray cast iron: This type is brittle but crack-resistant and has a gray appearance due to flaky graphite molecules. It offers increased wear resistance, low ductility, and high thermal conductivity.
- White iron: Highly wear-resistant, white iron is more brittle than other cast iron alloys due to the presence of hard carbides. The weldability of white iron can be improved with nickel-based fillers.
- Ductile iron: This alloy is augmented with magnesium, resulting in spherical graphite nodules. It offers superior tensile strength but is more brittle than gray cast iron. It is generally more weldable than gray cast iron.
- Malleable iron: Unlike other cast iron types, malleable iron is somewhat deformable and can bend. It is ductile and less prone to cracking compared to other types. However, it still benefits from a preheating phase.